Australian researchers have come up with a breakthrough new technique of making concrete, using old car tyres.
For all their importance to modern civilisation, tyres pose a big challenge when it comes to disposal at the end of their life, due to their durability, quantity, and material composition. But now, a team of engineers from the Royal Melbourne Institute of Technology (RMIT) University has taken concrete steps towards addressing this issue, as they’ve come up with a way to use discarded tyres to make concrete at a high enough level of quality that meets building codes.
A key component of concrete is aggregate – large particles such as gravel or crushed rock that gives the material its strength. The breakthrough process by the RMIT team manages to replace 100% of conventional aggregates with recycled rubber from used vehicle tyres.
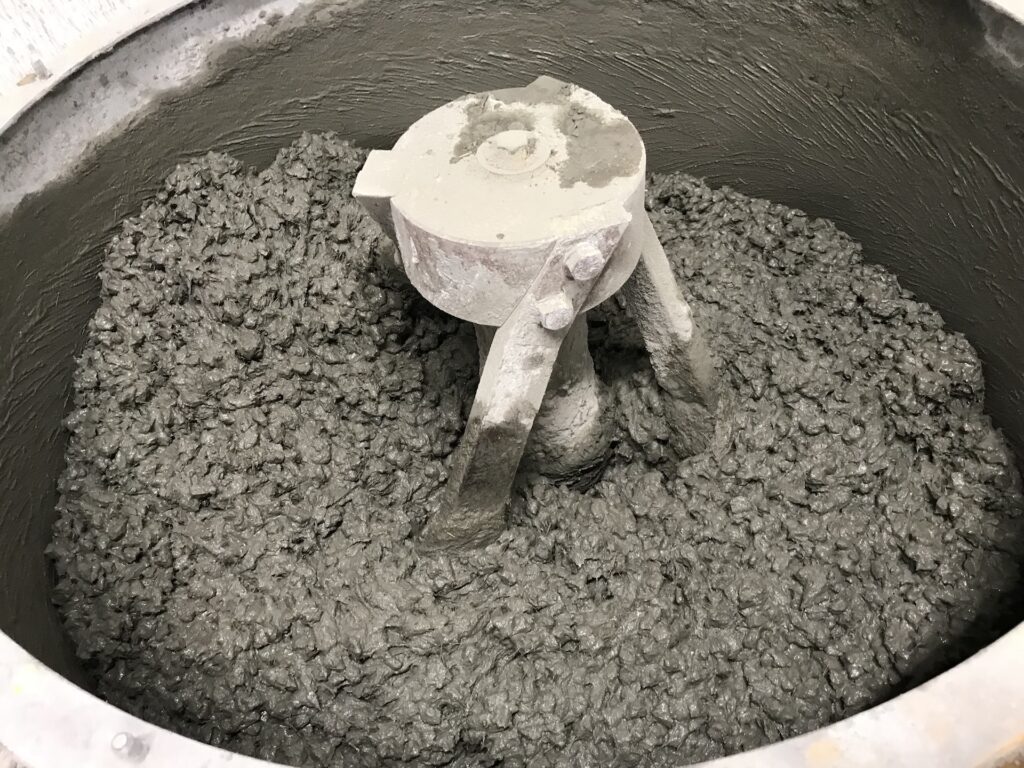
Small amounts of rubber are already currently used to supplement these aggregates, but attempts to completely replace aggregates with rubber have thus far resulted in concrete that was too weak.
Now, a new and precise casting method “compresses the coarse rubber aggregate in fresh concrete in a way that sufficiently enhances the material’s performance”, according to lead author and PhD researcher from RMIT University’s School of Engineering, Mohammad Momeen Ul Islam.
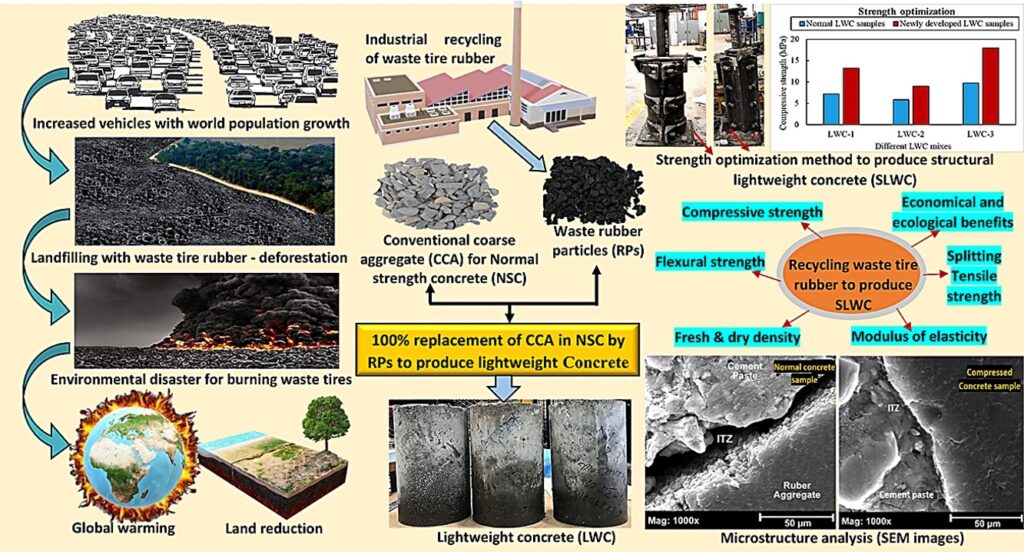
There are several benefits to this new innovation, both environmental and economical. For starters, not only does it help deal with the issue of used tyre disposal, it also greatly reduces the consumption of natural resources: aggregates are the most mined materials in the world.
More enticingly though, at least in the short term, is that this “rubber” concrete team is a lot lighter than conventional concrete with the same amount of strength, and this will bring big savings from manufacturing and transport costs, which will in turn benefit urban development, especially low-cost projects or in rural areas.
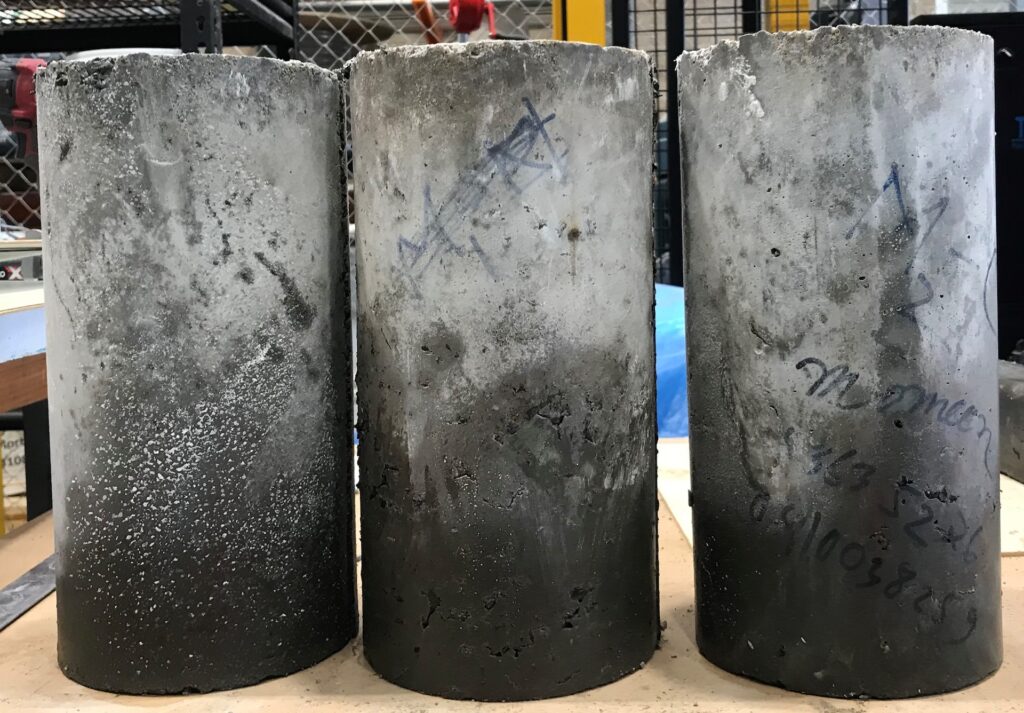
The team believes that the manufacturing process can be scaled up in a cost effective manner in existing precast concrete factories, and following successful testing in the workshop, they are now looking into reinforcing the concrete to see how it can work in structural elements.