This new disassembly process will help rev up the electric revolution and promote sustainability, and it’s all thanks to A*Star.
At the recent Industrial Transformation Asia-Pacific (ITAP) 2023 event, the Agency for Science, Technology, and Research (A*STAR) provided some exciting news. In their quest to revolutionize electric vehicle (EV) batteries, they’ve unveiled the Electric Vehicle Battery Testing and Disassembly Line.
With the wheels of transportation turning towards electrification, we find ourselves faced with a unique challenge – what to do with retired EV batteries?
Improper disposal is not an option. It not only poses threats to human health and the environment but squanders the valuable raw materials that can be recovered and given a second life. These retired batteries, despite their age, often have some useful life left in them, a second wind before they retire for good.
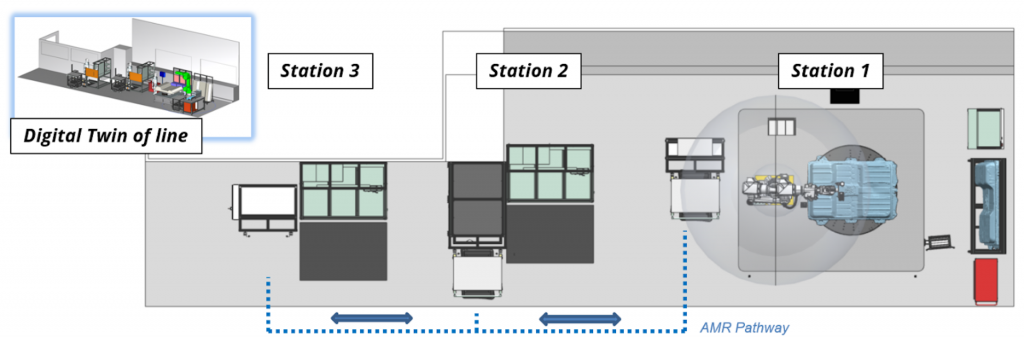
Now, disassembling an EV battery pack is no stroll in the park. They come in various shapes, sizes, physical conditions, and performance capabilities. It usually takes more than seven hours to manually dismantle a battery pack, and that’s only if you have a team of skilled hands working on it. Plus, there’s a pinch of danger when dealing with high-voltage cables, even if they’ve been discharged.
Now, here’s where A*STAR’s Electric Vehicle Battery Testing and Disassembly Line swoops in to save the day. It’s a fusion of the latest Industry 4.0 technologies, which include automation, robotics, intelligent vision inspections, and diagnostics. These tech-savvy wizards are here to make the disassembly process safer and more efficient. They can do what takes us seven hours in just half the time, thanks to automation, reducing human exposure to high-voltage risks.
Let’s talk about State-of-Health (SOH) – an essential indicator of a battery’s remaining useful life. The conventional method involves a complete charge and discharge cycle. But under A*STAR’s new line, they’ve shrunk the process down to just 30 minutes at the battery cell level. The line plans to scale this up further, evaluating both individual cells and modules to understand a module’s overall health.
Augmented reality (AR) guides employees through the testing and disassembly processes step by step. An energy management system optimizes the line’s energy usage, and automated guided vehicles (AGVs) ensure flexibility. Need more capacity? Just add more stations to check those battery packs’ physical conditions. It’s technology dancing with precision.
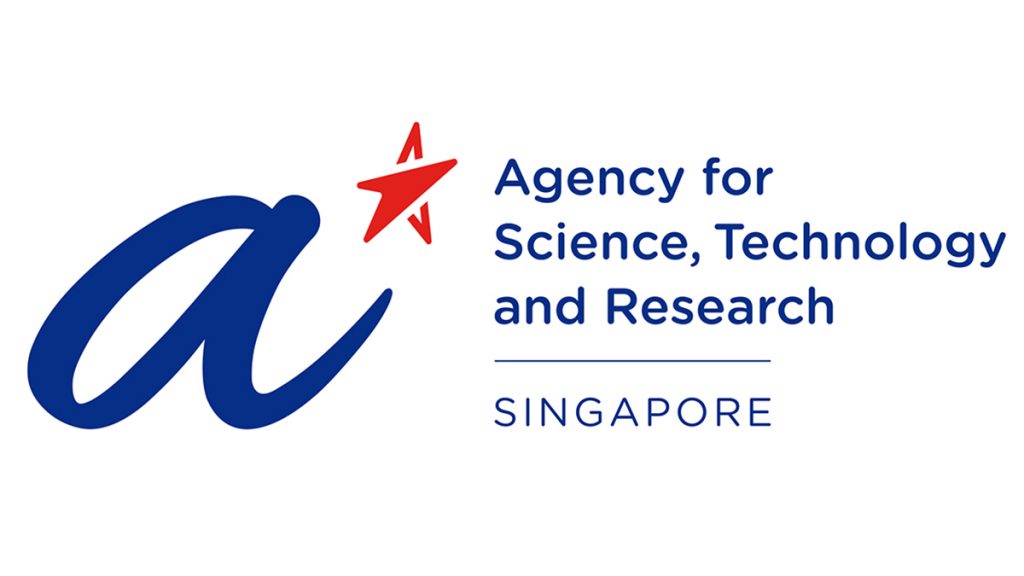
Dr David Low, CEO of ARTC, ASTAR, sums it up brilliantly, “ASTAR’s launch of the EV Battery Testing and Disassembly Line marks a significant milestone in our commitment to building a circular economy for batteries.” It’s not just about recycling; it’s about preserving the environment and paving the way for the future.
Kaushik Das, Managing Partner, Southeast Asia, McKinsey & Company, echoes the sentiment, “As electric vehicle (EV) adoption surges in the region, we need to be innovative in scaling digital solutions to better manage end-of-life (EOL) EV batteries.”
Check out more green rides here, or check out our latest videos on Ignition Labs TV!