Toyota is accelerating its factory decarbonisation efforts using renowned automotive Mirai technology.
Since June 2021, Toyota has been working with Fukushima Prefecture towards the development of new future cities using hydrogen. As part of these efforts, Toyota has attempted to use hydrogen along with renewable energy to decarbonise factories.
but how does this work?
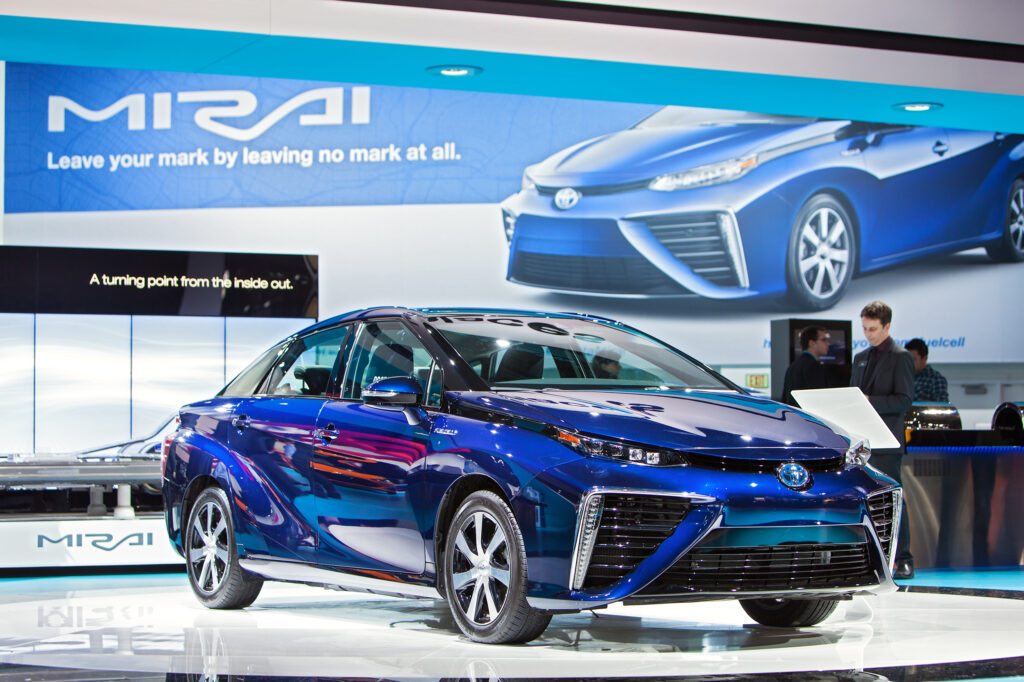
It all starts with the Toyota Mirai, a car developed to run on hydrogen. Electrolysis equipment within the vehicle produces hydrogen from electrolysing water. Retrofitting this technology on a larger scale, this system will be put into operation in March 2023 at a DENSO Fukushima Corporation plant. Plus, Toyota will accelerate its efforts by using electrolysis equipment to produce clean hydrogen, combusting it in one of the plant’s gas furnaces.
This hydrogen utilisation will be implemented as a project subsidised by the New Energy and Industrial Technology Development Organization (NEDO).
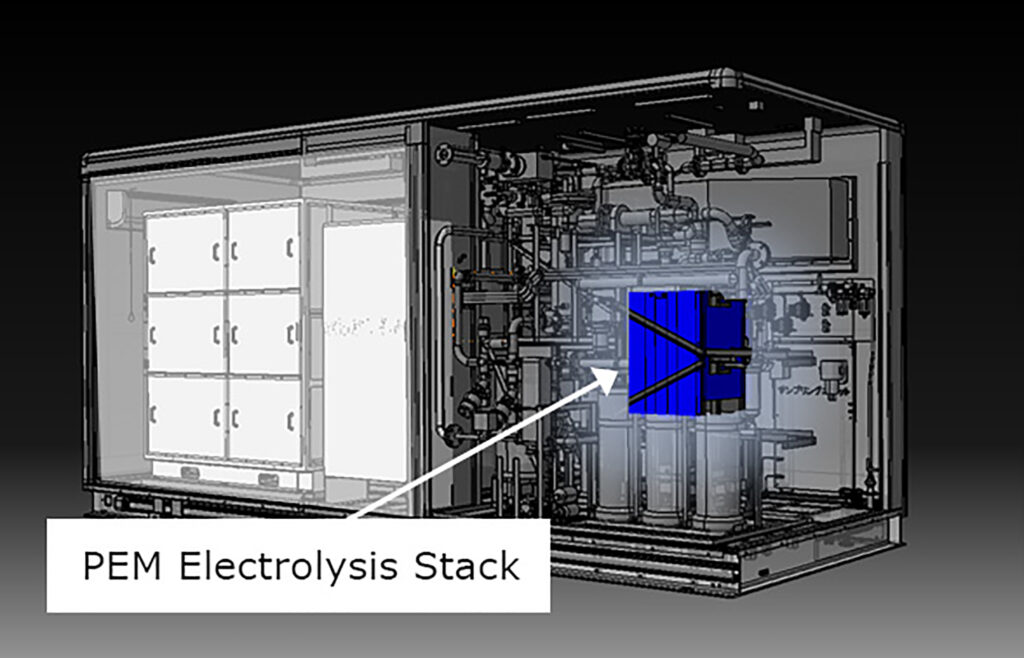
Factory decarbonisation efforts may very well be an effective alternative for promoting initiatives aimed at reducing CO2 emissions, and as a whole contributing to achieving carbon neutrality. Toyota aims to promote the use of hydrogen both through fuel cell electric vehicles (FCEVs), commercial trucks, and buses and also through the widespread use of fuel cell (FC) products. Examples of these include the development of FC stationary generators.
To this end, Toyota is working with various industry partners in the areas of producing, transporting, storing, and using hydrogen. This initiative is done in the hopes of expanding the technology to various industries and regions.
features of the electrolysis equipment.
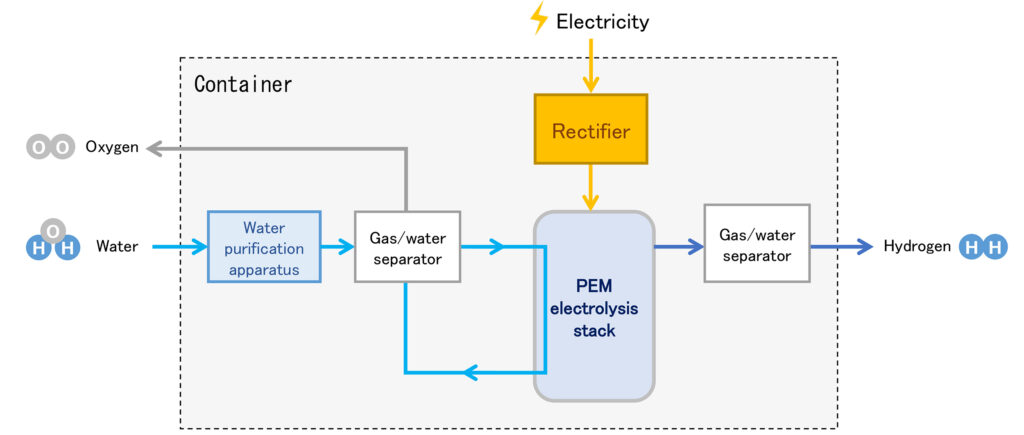
The electrolysis equipment is newly developed equipment that takes advantage of both the technology Toyota has cultivated over many years of FCEV development and the knowledge and expertise it has accumulated from a variety of usage environments around the world.
The cells used in the Proton Exchange Membrane (PEM) electrolysis stack are highly reliable, with a proven track record from the Toyota Mirai. Toyota has used titanium for the stack separator, which improves durability that is required of electrolysis equipment. This enables it to maintain almost the same level of performance even after 80,000 hours of operation. making it safe to use over a long period of time.
Plus, more than 90% of FC stack components can be shared in the PEM electrolysis stack production process. This eases mass production costs and significantly shortens the overall development period, as abundant knowledge and experience have already been accumulated over many years of FCEV development.
factory decarbonisation efforts as a whole.
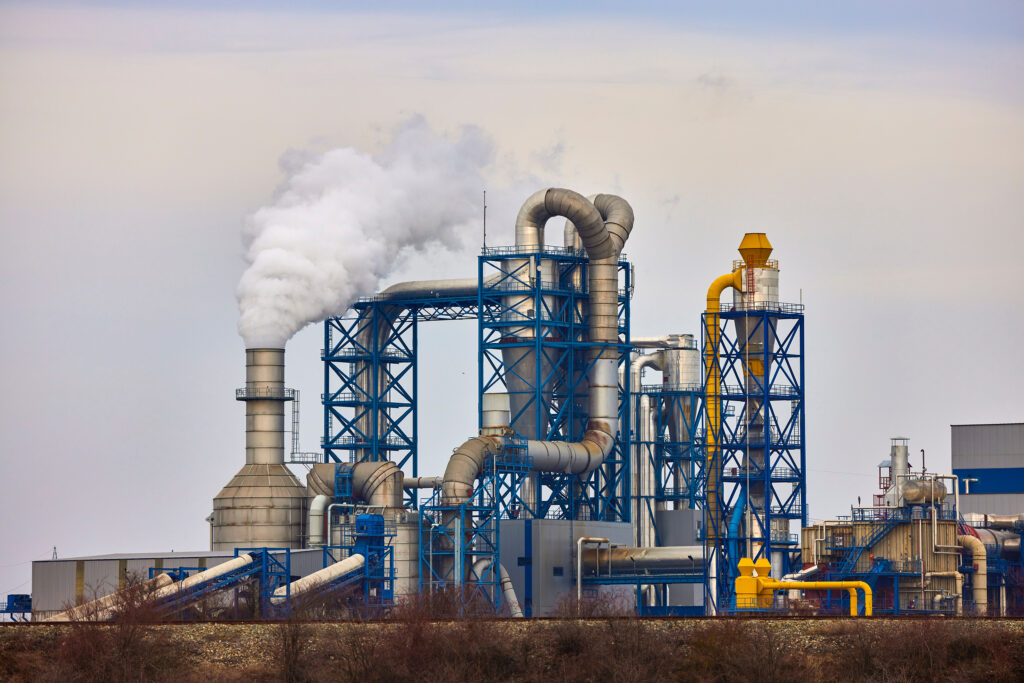
Scientific jargon aside, hydrogen is poised to be one of the best solutions to combat the rise of carbon emissions worldwide. Its clean energy returns can help factories reduce their carbon footprint massively, and still provide the energy needed to sustain daily life and activities.
This technology may still be in its infancy, but who’s to say it won’t kick off in the near future?
Read all about sustainability right here on Futr!